Chords for Banjo Assembly and Set-Up by Johnny Butten and Recording King
Tempo:
85.85 bpm
Chords used:
G
C
D#
F
Gm
Tuning:Standard Tuning (EADGBE)Capo:+0fret
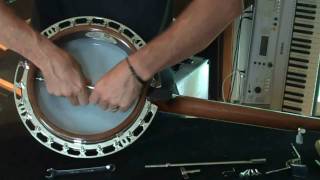
Jam Along & Learn...
Hey there, my name is Johnny Button, some of you may know me already.
I'm here in the studio today, we've got an RK75 Elite recording King Banjo.
We're just going to check it out, this is brand new, fresh out of the case,
here and see if we can,
any tweaks here and there to get a better sound out of it.
I'm sure there's room for a little bit of improvement in the setup.
to demonstrate the sound as it is,
that,
I'm here in the studio today, we've got an RK75 Elite recording King Banjo.
We're just going to check it out, this is brand new, fresh out of the case,
here and see if we can,
any tweaks here and there to get a better sound out of it.
I'm sure there's room for a little bit of improvement in the setup.
to demonstrate the sound as it is,
that,
100% ➙ 86BPM
G
C
D#
F
Gm
G
C
D#
_ _ Hey there, my name is Johnny Button, some of you may know me already.
I'm here in the studio today, we've got an RK75 Elite recording King Banjo.
We're just going to check it out, this is brand new, fresh out of the case,
and we're going to check it out here and see if we can,
we're going to tear it down, right down to the last nut and bolt,
and see if we can make any tweaks here and there to get a better sound out of it.
Sound out of the case isn't bad at all, it's a nice sounding banjo,
but I'm sure there's room for a little bit of improvement in the setup.
So I'm going to pick you a few bars of something just to demonstrate the sound as it is,
as I say, straight out of the case, and then we'll tear it down and film that,
and put it together and hopefully prove a point of getting it to sound a little bit better than it is now.
_ [G] _ _ [C] _ _ [Gm] _ _ _
_ [F#m] _ _ [G] _ _ _ [C] _ _
[E] _ _ _ _ [G] _ _ _ _
_ [C] _ _ [A] _ _ _ [D] _ _
_ [G] _ _ _ [C] _ _ [G] _ _
_ _ _ _ _ _ _ _
_ _ _ _ Okay, so here we are, we're going to start [N] stripping the banjo down.
You have four, generally speaking you have four, maybe three on some banjos, thumb screws.
Everything I do today will be referred to the Recording King Elite.
So on this we have four, I've already removed the two from the back here,
so we're just going to pull these.
If when you're playing you get any sound of vibration or like a buzzing,
these are usually the guys to blame.
They will vibrate loose if you haven't got them tweaked up.
I see a lot of guys playing with them loose, but they can be the source of some vibration when you're playing.
_ Okay, so with that, we can now lift the banjo free from the resonator,
set it down, I'll just put the resonator here for later on.
And now we're just going to tear the strings off this, _ I've already found a decent craftsmanship. _ _ _ _ _
Usually if the strings are dead, I'll just take a pair of cutters and cut straight through them.
But for the purposes of the video, we don't want to give anybody a cardiac arrest seeing the strings cut off in that way,
[Gm] so we'll do it a little bit [N] gentler this way. _ _ _ _ _ _ _
_ _ _ _ _ _ _ _
_ _ _ _ _ _ [F#] _ _
_ _ _ _ [N] _ _ Okay, so strings are loose, bridge comes off.
It's worthwhile noting while you've got the bridge in that position,
because of the different gauges in the strings, the fourth string being the thickest one,
just put a little five on the bottom of the string for where the fifth string goes.
That way you can guarantee getting the bridge the right way round every time.
If you happen to put it the wrong way round, well, the slot here for the fourth string is wider than any of the other strings,
so you may get the second string rattling in that slot or any of the other strings.
So just a little five underneath, that's the fifth string.
End for the bridge.
_ And once that's [D#] done, you can flip the top, pull on any of the [G] strings. _
_ These are just linked into the little side _ clamps here, so they just pop out.
[D#] The third string should just slide through.
[N] So there we go, we've got a set of strings off the banjo.
And we won't be using these anymore.
A recording can use, but invariably most banjo companies will use a cheaper grade of string.
So the first thing I did was trash the strings that it came with.
_ So there [F#] they are.
We will replace those [G#] later with a brand of my choice, a string I've used for _ about 30 years.
Just taking the nut off the bottom of the tailpiece bolt there.
Very simple, _ straightforward.
Put it off for safekeeping and put it with the rest of your parts.
OK, the basic tools we're going to need is a 7-6-16 wrench,
the bracket wrench that comes with the banjo,
and a small hex key or Allen key. _
_ So we're just going to have a single bolt [G] on the armrest here.
And that's just kind of a sandwich deal.
There's a plate in behind which is [N] threaded.
And as you tighten it up, it just clamps itself against the tension brackets.
So I'm just going to pull that and take this plate out. _ _ _ _ _ _
And again, put things back together.
That way bolts don't get lost, fittings don't get lost.
Not only can that be very irritating, but if you don't find it, it becomes more costly.
You can't see it already.
So there's that.
We can now flip this over.
I'm not going to remove the tuners.
There's no reason to actually remove them.
They're not going to gain any tone or anything.
Needless to say, just check they're pretty tight in there.
Sometimes a tuner nut can vibrate loose.
I've had it happen on tour. _
So now we need to take the neck off the bottom of the banjo, off the pot.
_ You have these called coordinator rods.
Basically there's a lag bolt that comes out of the neck, which we'll see in a minute.
That one's threaded.
These tubes then screw onto that to secure the neck.
And then we have three nuts here.
This one is fairly light pressure just to _ engage it with the rim.
Actually it's only finger [E] tight on this particular banjo, which again would be another source of vibration.
And obviously isn't secure in the neck 100%.
So we'll rectify that when we rebuild.
And then you have kind of a sandwich effect here.
Basically once this rod is as tight as you want it, just pull this one up against the rim so it's fairly snug.
And then this one.
Or you can use two wrenches and do it equal.
You don't want either [B] of the inside ones [A] tightened against the rim too much.
Because that will in fact actually [D] distort the rim.
Which will lead to bigger problems at a later date with fitting the flange and all that kind of stuff.
[D#] Months, maybe even years down the [N] line.
But it will actually distort the rim.
So all we're going to do here, we're going to loosen off this bottom nut and the inside one.
Just make sure they're good.
And we'll give this one plenty of release on the thread.
Because we're going to need to undo it from this end and pull it back. _
Also the model in here is actually threaded this end so we can avoid how much we have to actually pull it back on other banjos.
Which would just be a one piece coordinator rod with no thread. _
Obviously less adjustment.
Make sure all your parts go [F#m] together. _ _
This one [F] here as I say isn't [N] really finger tight anyway. _ _ _
Big problem with that.
And the coordinator rod itself is only finger tight against the neck.
So in my opinion that's a hampering tone because it's not as solid a construction with the neck as it would be.
Again this is very loose.
I think I'll have to tweak the nut so it's a good firm joint.
There's a lot of time and effort put into cutting the neck joint.
So it's a good joint with the pop.
And it seems rather silly to me to not have it tweaked [F] up nice and tight.
So that neck [N] joint will be as secure as possible.
Okay so there's our second coordinator rod.
Now our next thing is to pull out the pop.
A couple of washers just gone in there.
So [F] take note of those.
Make sure you [N] keep those.
And now you've got your pop assembly.
We'll pull it out of here.
I'm here in the studio today, we've got an RK75 Elite recording King Banjo.
We're just going to check it out, this is brand new, fresh out of the case,
and we're going to check it out here and see if we can,
we're going to tear it down, right down to the last nut and bolt,
and see if we can make any tweaks here and there to get a better sound out of it.
Sound out of the case isn't bad at all, it's a nice sounding banjo,
but I'm sure there's room for a little bit of improvement in the setup.
So I'm going to pick you a few bars of something just to demonstrate the sound as it is,
as I say, straight out of the case, and then we'll tear it down and film that,
and put it together and hopefully prove a point of getting it to sound a little bit better than it is now.
_ [G] _ _ [C] _ _ [Gm] _ _ _
_ [F#m] _ _ [G] _ _ _ [C] _ _
[E] _ _ _ _ [G] _ _ _ _
_ [C] _ _ [A] _ _ _ [D] _ _
_ [G] _ _ _ [C] _ _ [G] _ _
_ _ _ _ _ _ _ _
_ _ _ _ Okay, so here we are, we're going to start [N] stripping the banjo down.
You have four, generally speaking you have four, maybe three on some banjos, thumb screws.
Everything I do today will be referred to the Recording King Elite.
So on this we have four, I've already removed the two from the back here,
so we're just going to pull these.
If when you're playing you get any sound of vibration or like a buzzing,
these are usually the guys to blame.
They will vibrate loose if you haven't got them tweaked up.
I see a lot of guys playing with them loose, but they can be the source of some vibration when you're playing.
_ Okay, so with that, we can now lift the banjo free from the resonator,
set it down, I'll just put the resonator here for later on.
And now we're just going to tear the strings off this, _ I've already found a decent craftsmanship. _ _ _ _ _
Usually if the strings are dead, I'll just take a pair of cutters and cut straight through them.
But for the purposes of the video, we don't want to give anybody a cardiac arrest seeing the strings cut off in that way,
[Gm] so we'll do it a little bit [N] gentler this way. _ _ _ _ _ _ _
_ _ _ _ _ _ _ _
_ _ _ _ _ _ [F#] _ _
_ _ _ _ [N] _ _ Okay, so strings are loose, bridge comes off.
It's worthwhile noting while you've got the bridge in that position,
because of the different gauges in the strings, the fourth string being the thickest one,
just put a little five on the bottom of the string for where the fifth string goes.
That way you can guarantee getting the bridge the right way round every time.
If you happen to put it the wrong way round, well, the slot here for the fourth string is wider than any of the other strings,
so you may get the second string rattling in that slot or any of the other strings.
So just a little five underneath, that's the fifth string.
End for the bridge.
_ And once that's [D#] done, you can flip the top, pull on any of the [G] strings. _
_ These are just linked into the little side _ clamps here, so they just pop out.
[D#] The third string should just slide through.
[N] So there we go, we've got a set of strings off the banjo.
And we won't be using these anymore.
A recording can use, but invariably most banjo companies will use a cheaper grade of string.
So the first thing I did was trash the strings that it came with.
_ So there [F#] they are.
We will replace those [G#] later with a brand of my choice, a string I've used for _ about 30 years.
Just taking the nut off the bottom of the tailpiece bolt there.
Very simple, _ straightforward.
Put it off for safekeeping and put it with the rest of your parts.
OK, the basic tools we're going to need is a 7-6-16 wrench,
the bracket wrench that comes with the banjo,
and a small hex key or Allen key. _
_ So we're just going to have a single bolt [G] on the armrest here.
And that's just kind of a sandwich deal.
There's a plate in behind which is [N] threaded.
And as you tighten it up, it just clamps itself against the tension brackets.
So I'm just going to pull that and take this plate out. _ _ _ _ _ _
And again, put things back together.
That way bolts don't get lost, fittings don't get lost.
Not only can that be very irritating, but if you don't find it, it becomes more costly.
You can't see it already.
So there's that.
We can now flip this over.
I'm not going to remove the tuners.
There's no reason to actually remove them.
They're not going to gain any tone or anything.
Needless to say, just check they're pretty tight in there.
Sometimes a tuner nut can vibrate loose.
I've had it happen on tour. _
So now we need to take the neck off the bottom of the banjo, off the pot.
_ You have these called coordinator rods.
Basically there's a lag bolt that comes out of the neck, which we'll see in a minute.
That one's threaded.
These tubes then screw onto that to secure the neck.
And then we have three nuts here.
This one is fairly light pressure just to _ engage it with the rim.
Actually it's only finger [E] tight on this particular banjo, which again would be another source of vibration.
And obviously isn't secure in the neck 100%.
So we'll rectify that when we rebuild.
And then you have kind of a sandwich effect here.
Basically once this rod is as tight as you want it, just pull this one up against the rim so it's fairly snug.
And then this one.
Or you can use two wrenches and do it equal.
You don't want either [B] of the inside ones [A] tightened against the rim too much.
Because that will in fact actually [D] distort the rim.
Which will lead to bigger problems at a later date with fitting the flange and all that kind of stuff.
[D#] Months, maybe even years down the [N] line.
But it will actually distort the rim.
So all we're going to do here, we're going to loosen off this bottom nut and the inside one.
Just make sure they're good.
And we'll give this one plenty of release on the thread.
Because we're going to need to undo it from this end and pull it back. _
Also the model in here is actually threaded this end so we can avoid how much we have to actually pull it back on other banjos.
Which would just be a one piece coordinator rod with no thread. _
Obviously less adjustment.
Make sure all your parts go [F#m] together. _ _
This one [F] here as I say isn't [N] really finger tight anyway. _ _ _
Big problem with that.
And the coordinator rod itself is only finger tight against the neck.
So in my opinion that's a hampering tone because it's not as solid a construction with the neck as it would be.
Again this is very loose.
I think I'll have to tweak the nut so it's a good firm joint.
There's a lot of time and effort put into cutting the neck joint.
So it's a good joint with the pop.
And it seems rather silly to me to not have it tweaked [F] up nice and tight.
So that neck [N] joint will be as secure as possible.
Okay so there's our second coordinator rod.
Now our next thing is to pull out the pop.
A couple of washers just gone in there.
So [F] take note of those.
Make sure you [N] keep those.
And now you've got your pop assembly.
We'll pull it out of here.